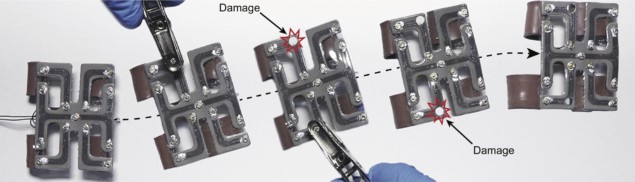
A new metal-elastomer composite automatically self-heals by creating new electrical connections that bypass damaged areas. The material, which repairs itself in a process that is somewhat analogous to plasticity in nervous tissue, might be used to make stretchable circuits, soft machines, bio-inspired robots and wearable electronics that won’t suddenly fail when mechanically damaged.
“I’ve always been fascinated by neuroplasticity and the way that neurons can form new synaptic networks to bypass diseased or damaged tissue,” says Carmel Majidi from Carnegie Mellon University in the US, who led this research effort. “While we haven’t fully mimicked neuroplasticity here, this process was a helpful source of inspiration for developing and understanding our material.”
Soft and deformable circuits
Researchers have made great strides in developing soft and deformable circuits, mainly from soft conductive polymers, conductive fluids in gels and soft microfluidic channels. These materials can be used to make highly flexible, stretchable and conformable electronics that work as artificial skin and nervous tissues in a wide range of innovative applications, from second-skin wearable computers to bio-inspired robots. However, the problem is that these soft elastic structures can easily tear, puncture or mechanically fail, which ultimately means loss in electrical conductivity.
The new material is made of a soft silicon rubber embedded with micron-sized droplets of a gallium-indium based metal alloy that is liquid at room temperature. “To trace circuits in this structure, we use a pen plotter that ruptures the droplets and makes them coalesce into electrically-conductive lines along the pen path,” explains Majidi. “Since the material is mechanically compliant, the resulting circuit is also highly stretchable and as soft as natural skin.
New conductive pathways
“When a circuit trace is damaged, the liquid droplets around the damaged area rupture and form new conductive pathways to bypass the damaged area and re-route electrical signals without interruption. The new pathways form spontaneously on their own and allow the circuit to remain functional. Such electrical ‘self-healing’ is especially important for circuits that are soft and stretchable since, like natural biological tissue, they need to be resilient to cuts, punctures and bruising loads.”
The material could be useful for robust circuit wiring in stretchable textiles and inflatable structures, Majidi tells Physics World. Some examples include sensor-containing garments for wearable computing, or even inflatable houses and airships that are integrated with damage-resistant electrical wiring.
Towards artificial nervous tissue
“Looking longer-term, we believe it might be used as artificial nervous tissue for soft machines and robots that mimic soft natural organisms able to physically interact with humans in a safe way. As with natural nervous tissue, the self-healing circuitry would be resilient to damage and allow the robot to withstand extreme loads and real-world conditions.”
Indeed, the researchers say they have already demonstrated the unprecedented robustness of their material in a self-repairing digital counter and a self-healing soft robotic quadruped that continues to function even after being damaged quite seriously.
The Carnegie Mellon team now plans to engineer and study soft conductive materials capable of both spontaneous electrical and mechanical self-healing. “While electrical self-healing is an important property, our material cannot repair itself mechanically after damage,” says Majidi. “A structure that can do both would bring us even closer to fabricating machines and electronics that are as extraordinarily resilient as natural biological tissue.”
The electrically self-healing liquid metal-elastomer composite is detailed in Nature Materials.